40 درصد صرفه جویی ارزی در ساخت کمپرسور ایرانی برای صنعت فولاد
به گزارش وبلاگ ساعتچی، تهران (پانا) - در مراسم امضای تفاهم نامه همکاری شرکت فولاد اقلید پارس برای ساخت ماشین آلات فولادی در داخل کشور مطرح شد که ساخت هر کمپرسور فولادسازی در ایران می تواند صرفه جویی ارزی 350 هزار یورویی در پی داشته باشد.
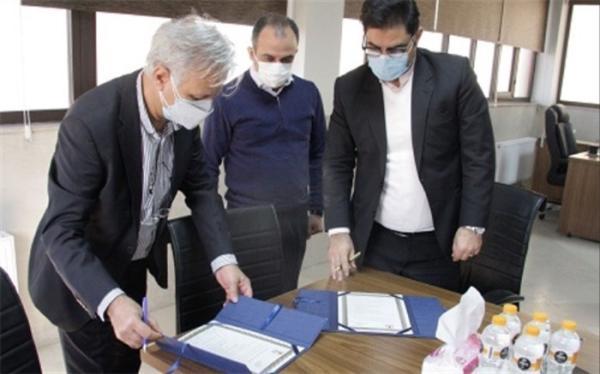
در پی برنامه بومی سازی، ساخت داخل کردن و طراحی و ساخت کمپرسورها و قطعات موردنیاز صنعت فولاد در شرکت پیشگامان صنایع آسیا، قیمت پیشنهادی برای ساخت کمپرسورهای واحدهای احیاء مستقیم 40 درصد پایین تر از نمونه مشابه خارجی بوده و شرکت های داخلی به جای پرداخت 900 هزار یورو بابت خرید خارجی و چند ماه اتلاف وقت برای ثبت سفارش و حمل ونقل و انتقال ارز، با صرفه جویی 350 هزار یورو می توانند کمپرسورهای موردنیاز خود را از طریق شرکت های داخل کشور تأمین کنند.
در این راستا، رضا شریفی مدیرعامل شرکت فولاد اقلید پارس در بازدید از شرکت پیشگامان صنایع آسیا، تفاهم نامه، همکاری بین دو شرکت فولاد اقلید پارس و شرکت پیشگامان صنایع آسیا را با مهندس حمیدرضا آستانه، مدیرعامل این شرکت در زمینه ساخت، تعمیرات، خدمات پس از فروش و همچنین تأمین قطعات یدکی کمپرسورهای فوق الذکر به امضا رساندند.
علیرضا نظری، پیشگامان و پیشکسوت در صنعت فولاد و مدیرعامل کارخانه در این مراسم با اشاره به صرفه جویی قابل توجه 40 درصدی در ساخت کمپرسورهای صنعت فولاد گفت: علاوه بر صرفه جویی ارزی ساخت کمپرسورها در داخل کشور، در زمینه بازسازی کمپرسورهای قدیمی نیز امکان صرفه جویی بسیاری فراهم شده و کمپرسورهای قدیمی تنها با مبلغی معادل 10 درصد قیمت خرید کمپرسورهای نو، بازسازی شده و به خط تولید برمی گردند.
نظری اضافه نمود: تقریباً با 10 درصد قیمت اولیه خرید کمپرسور ها کار بازسازی کمپرسورها اجرا شده و به مجموعه تولید برمی گردند و در ایام تحریم و مسائل مالی، کار بازسازی کمپرسورها عددی نزدیک به 750 میلیارد تومان صرفه جویی برای صنعت کشور داشته است.
750 میلیارد تومان صرفه جویی با تعمیر و بازسازی 30 کمپرسور
این پیشکسوت صنعت فولاد، اضافه نمود: ساخت کامل کمپرسور در ایران حداقل 40 درصد صرفه جویی ارزی برای کشور به همراه خواهد داشت یعنی قیمت 900 هزار یورو با این صرفه جویی تا 550 هزار یورو کاهش یافته و در اختیار مصرف کننده صنعت قرار می گیرد. پس از سال ها تلاش در این عرصه و با استفاده از توان کارشناسان داخلی به دانش ساخت کمپرسورها دست یافته و با استفاده از این دانش کشور را در این عرصه بی نیاز خواهیم کرد.
وی اضافه نمود: قیمت خرید این کمپرسورها از خارج در حال حاضر نزدیک به 30 میلیارد تومان بوده در راستای صرفه جویی ارزی این کمپرسور را با استفاده از دانشی که داریم بازسازی می کنیم. مبلغ صرف شده برای بازسازی، حدود 10 درصد مبلغ کل کمپرسور است و پس از بازسازی این کمپرسور مجدداً به چرخه تولید در صنایع فولاد کشور برمی شود. نزدیک به 30 کمپرسور را تعمیر و بازسازی کردیم و به صنعت برگردانیم که صرفه جویی ریالی آن نزدیک به 750 میلیارد تومان برای صنایع فولاد کشور بوده است.
مهندس نظری با اشاره به اینکه هیچ کارخانه ای در دنیا تمام قطعات موردنیاز را نمی سازد و بر اساس صرفه مالی، دانش طراحی و ساخت و انتقال دانش فنی بخشی از قطعات را تولید و بخش دیگر را وارد می کند، گفت: بر این اساس، سیستم های ابزار دقیق و گیربکس های این کمپرسورها از خارج تهیه می شود که برای بومی سازی این قطعات و یا تجهیزات می توان از توانایی شرکت های دیگر ایرانی بهره برد. ما در ایران دانش ساخت کمپرسورهای واحدهای احیای مستقیم فولادسازی را داریم و در آینده از واردات این گونه تجهیزات بی نیاز خواهیم شد.
مهندس نظری گفت: کیفیت قطعه سازی در این شرکت مطلوب بوده و تولید قطعات بر اساس استانداردهای جاری در صنعت فولاد انجام می پذیرد و همچنین قیمت تمام شده برای مشتری از خرید خارجی کمتر است؛ به عبارت دیگر، خدمات با کیفیت مطلوب، قیمت کمتر و در زمان های بسیار کوتاه نسبت به تأمین آن ها از خارج از کشور در حال ارائه به کارفرمایان محترم است.
350 هزار یورو صرفه جویی ساخت هر کمپرسور فولادسازی در ایران
نظری با اشاره به سابقه طولانی خود و مهندس آستانه در واحدهای فولادسازی کشور و بومی سازی و انتقال دانش فنی گفت: انتقال دانش فنی طراحی و ساخت واحدهای احیاء مستقیم از کشورهای مختلف اجرا شده و در حال حاضر برای طراحی این واحدها هیچ گونه نیازی به خارج از کشور نداریم. بیش از 70 درصد تجهیزات این واحدها در ایران ساخته شده و با تولید این کمپرسورها و چند تجهیز دیگر این عدد به بیش از 80 درصد خواهد رسید.
وی گفت: بخش اعظم مواد نسوز واحدهای احیاء در ایران تولید می شود همچنین کاتالیست ها کاملاً بومی سازی شده اند و با بومی سازی کمپرسورها وابستگی به خارج از کشور به کمتر از 10 درصد خواهد رسید.
با توجه به عمر واحدهای احیاء در ایران به تدریج هزینه تعمیر و نگهداری کمپرسورها بالا خواهد رفت و بازسازی کمپرسورها در ایران چه به لحاظ زمان کارکرد واحد و چه از جهت صرفه جویی مالی بسیار اثرگذار خواهد بود.
آستانه: 60 درصد مواد اولیه ساخت قطعات در ایران تولید می شود
آستانه مدیرعامل شرکت پیشگامان صنایع آسیا در این مراسم گفت: تمام دغدغه مدیران و صنعتگران از ابتدای جمهوری اسلامی تا الآن همین بوده که هرچقدر می توانیم، وابستگی به خارج را کم کنیم.
وی اضافه نمود: در این دوره ای که در ایران قطعه تولید کردیم و به شرکت های فولادی دادیم عملاً فولادی ها تمایل ندارند از خارج خرید کنند چون با توجه به کیفیت قطعات که کاملاً مطلوب بوده تمایل به تأمین قطعات و بازسازی در داخل دارند. خوشبختانه حتی یک مورد برگشت قطعه و بازسازی ها را از فولادسازی ها نداشتیم و همه رضایت داشته اند و 100 درصد مثبت بوده است و قیمت تمام شده برای مشتری خیلی پایین تر از خرید خارج است. همچنین ما سرویس خدمات پس از فروش به موقع می دهیم یعنی ما در انبار قطعات یدکی تولید خود را داریم و به محض و اعلام نیاز، قطعه آن ها بلافاصله تأمین می شود؛ و این حسن بزرگی است که نمی خواهند منتظر تولید قطعه باشند.
شریفی مدیرعامل شرکت فولاد اقلید، در پاسخ گفت: بله، درگذشته بین دو تا سه سال طول می کشید تا قطعات وارد شود و ماشین آلات وارد شود و هزینه فرصت و پول و دلار زیادی خرج می شد تا کار انجام شود؛ اما اکنون بسیاری از قطعات و ماشین آلات با هزینه کمتر در داخل انجام می شود.
آستانه گفت: در حال حاضر حدود 50 الی 60 درصد مواد اولیه برای تولید قطعات و ماشین آلات نیز در ایران تأمین می شود و به زودی به 100 درصد می رسد؛ کل مواد اولیه استیل هم در ایران تولید خواهد شد.
شریفی نیز گفت: چه هزینه عظیمی در سه سال گذشته برای ثبت سفارش، واردات، نصب، واریز وجه و انتقال ارز به صنعت تحمیل می شد تا آن شرکت سازنده اصلی بتواند قطعه را تأمین کند. گاهی اعلام می کردند که فعلاً نداریم و باید منتظر باشید تا چند سال دیگر تأمین کنیم؛ اما حالا از فناوری و دانش بومی خود استفاده می کنیم و این قرارداد همکاری پایه ای خواهد شد برای سایر فولادسازان که در بومی سازی و تأمین قطعات پیروز شوند و با هزینه کمتر به درخواست های خود پاسخ دهند.
طرح های فولادی کشور به خاطر تأخیر طولانی در بهره برداری، از صرفه و توجیه مالی خارج می شدند
مدیرعامل شرکت فولاد اقلید اضافه نمود: تقریباً 7 پروژه را هم زمان با ما آغاز می کنند و قبل از اینکه ثبت سفارش خارجی به نتیجه برسد و قطعه وارد شود، ما از طریق بومی سازی و ساخت داخل می توانیم نیازهای خود را تأمین کنیم.
شریفی از مجری طرح های احیای فولادی، ادامه داد: از سال 86 که هشت طرح فولادی کشور آغاز شد، از ابتدا با 2 سال کندی در مراحل توسعه و ساخت همراه بود که به تدریج با مسائل نو و تحریم ها روبرو شد.
وی با بیان اینکه بعد از آغاز هفت طرح فولادی کشور در سال های اخیر، تحولاتی در صنعت فولاد رخ داده است، اضافه نمود: در پی تحریم ها قیمت ها بالا رفت و درخواست های خرید و تعمیرات از شرکت های خارجی پذیرفته نمی شد و درنتیجه راه چاره داخلی سازی پیگیری شد و به تدریج کارگاه ها و شرکت های بیشتری در راستا ساخت داخل قرار گرفتند؛ چراکه واردات قطعات و ماشین آلات موردنیاز صنعت فولاد به خاطر کاربرد دوگانه آن ها متوقف شد و باوجود تعهد شرکت های سازنده آمریکایی، آلمانی، ژاپنی و... عملاً تأمین قطعات و ماشین آلات و تعمیرات و خدمات پس از فروش آن ها با کارشکنی هایی روبرو شد و نیازهای داخل ایران و فولادسازی ها تأمین نشد.
این فعال حوزه فولاد و آهن اسفنجی، با اشاره به اینکه طرح های فولادی کشور به خاطر تأخیر طولانی در بهره برداری از آن ها عملاً با خارج شدن از صرفه مالی و توجیه مالی روبرو می شدند، شرح داد: درنتیجه همکاران و مدیران و کارکنان فولادسازی، به این فکر افتادند که برای تعمیرات و تأمین قطعات، باید بومی سازی کنند و در ساخت ماشین آلات نیز نیاز به صنایع داخلی افزایش یافت و شرکت های داخلی، متخصصان و نخبگان برای بومی سازی، انتقال دانش فنی، مهندس معکوس و ساخت و تأمین قطعات و ماشین آلات برنامه ریزی کردند، لذا بحث اساسی در واحدهای احیا بومی سازی بوده است و ما به عنوان کارفرما و مجری، در پی این بوده ایم که موضوع بومی سازی قطعات و ماشین آلات، باثبات و امنیت بیشتری همراه شود.
مدیرعامل شرکت فولاد اقلید با بیان اینکه، در فولاد اقلید سعی خواهد شد بیشترین استفاده از منابع داخلی صورت بگیرد تا متعاقب آن کمترین وابستگی به خارج فراهم شود، اضافه نمود: مجری پروژه اقلید در پی آن است که برای ساخت واحد فولادسازی با ظرفیت 1 میلیون تن، کمپرسورها بومی سازی شود و وابستگی به خارج کمتر باشد؛ بر این اساس با شرکت پیشگامان صنایع آسیا، این تفاهم نامه همکاری را امضا کرده ایم.
شریفی با تأکید بر اینکه برنامه بومی سازی و داخلی سازی در صنعت فولاد در بخش های مختلف از احیای مستقیم تا اسلب، نورد و سایر رشته ها، آغاز شده و مطالعات بازار اجرا شده است، گفت: تعدادی از مهندسان ما که در خارج از کشور آموزش دیده اند، اتفاقات و تحولات ویژه ای را ایجاد کرده اند و در صنعت فولاد کشور کار کرده و حتی در دوره جنگ نیز در خط مقدم کار و صنعت بوده اند، در احیای کشور باید از دانش و تجربه آن ها استفاده کنیم.
وی با اشاره به برنامه چشم انداز تولید 54 میلیون تن فولاد تا سال 1404، گفت: برنامه افزایش تولید و ظرفیت سازی فولاد عقب افتاده اما به تدریج به این ظرفیت نزدیک خواهیم شد. برنامه تولید 37 میلیون تن گندله سازی و 38 میلیون تن آهن اسفنجی به همراه برنامه اشتغال زایی در صنعت فولاد در دستور کار قرارگرفته و مدیران صنعت فولاد برای ایجاد ظرفیت های بزرگ تولید در منطقه هرمزگان و کنار آب برنامه ریزی کرده اند.
مدیرعامل شرکت فولاد اقلید پارس، با اشاره به اهمیت توسعه بالادستی کنسانتره، گندله سازی و ظرفیت تولید سنگ آهن و مواد اولیه، شرح داد: یک کنسرسیوم بزرگ فولادی در شرکت صنایع فلزات کشور برنامه تولید پایدار کنسانتره را در 10 سال آینده هدف قرار داده است.
آستانه: تولید قطعات ماشین آلات فولاد با برند ایرانی در سه سال آینده
حمیدرضا آستانه، مدیرعامل شرکت پیشگامان صنایع آسیا نیز در این مراسم گفت: شرکت پیشگامان از 4 سال پیش آغاز به ساخت قطعات کمپرسورها کرده و در حال حاضر به فنّاوری ساخت این تجهیزات دسترسی کامل پیداکرده است و آمادگی این را دارد که به صورت کامل این تجهیزات را تولید کند.
وی همچنین اضافه نمود: خودمان قطعات را تولید کرده و کل فولاد ایران از این قطعات یدکی استفاده می کنند، علاوه بر آن بازسازی کمپرسورها را انجام می دهیم که کمپرسورهای فرسوده در مجموعه ما بازسازی می شوند و به خط تولید برمی گردند.
آستانه گفت: قدم بعدی ساخت کامل تجهیزات تولید است که برنامه ساخت آن از 2 ماه پیش آغاز شده است؛ و تا انتها سال آینده تجهیزات کامل را در واحدهای فولاد بهره برداری می کنیم.
وی با اشاره به رعایت استانداردهای بین المللی در ساخت قطعات و کمپرسورها، اضافه نمود: ازلحاظ رعایت استاندارد نیز ما تحت لیسانس کار نمی کنیم، بلکه استانداردهای بین المللی را رعایت می کنیم؛ بدین صورت که در مرحله اول برنامه مهندسی معکوس و طراحی مجدد این تجهیزات را با توجه به دانش اصلی شرکت های خارجی داریم و در مراحل بعدی برنامه تولید تجهیزات با برند ایرانی را خواهیم داشت که برنامه 3 سال آینده است.
مدیرعامل شرکت پیشگامان، تأکید کرد: در 3 سال آینده همه قطعات با برند پیشگامان صنایع آسیا و بر اساس استانداردهای بین المللی تولید و نیازها و درخواست های کمپرسور برای واحدهای تولیدی را تأمین خواهیم کرد.
آستانه، گفت: در صنعت ایران ماشین سازی برای خطوط تولید، یکی از پیچیده ترین بخش های صنعت محسوب می شود و به خاطر همین ماشین سازهای بین المللی در آمریکا، ژاپن و آلمان مستقر هستند و آخرین دستاوردها و فناوری ها را در امور ماشین سازی به کار می گیرند و فولادسازی ها در ایران ماشین های خود مانند کمپرسورها را از این کشورها وارد کرده و نصب کرده اند.
وی با بیان اینکه، کمپرسورهای واحد احیای مستقیمی که در قلب کارخانه فولاد با روش احیای مستقیم قرار گرفته است، حاصل فناوری های آمریکا، ژاپن و آلمان است، اضافه نمود: بازسازی کمپرسورهای فرسوده در مجموعه پیشگامان صنایع آسیا انجام می شود و از شرکت های مختلف فولادسازی کشور ازجمله خراسان، هرمزگان و مبارکه، کمپرسورها به این کارخانه وارد و تعمیرات آن ها انجام می گیرد و قطعات موردنیاز آن ها ساخته می شود.
وی در پاسخ به این پرسش که آیا استانداردهای دنیای را نیز دریافت می کند گفت: برای آنکه دانش بومی ساخت کمپرسور در ایران استاندارد دنیای بگیرد برای ثبت برند پیشگامان صنایع آسیا اقدام خواهد شد و این برند نشانه دریافت استانداردهای دنیای و ساخت داخل کردن کمپرسورهای واحدهای احیای مستقیم در فولادسازی است. این کار در سه سال آینده انجام خواهد شد و برند پیشگامان با رعایت استانداردهای دنیای به ثبت خواهد رسید.
زمان تأمین بخش عمده قطعات سه هفته پیش بینی شده است
علیرضا نظری مدیر کارخانه پیشگامان و پیشکسوت در صنعت فولاد نیز در ادامه گفت: ما گواهی های رضایت مندی را از کارفرمایان دریافت کرده ایم و در حال حاضر در قالب قرارداد با شرکت فولاد مبارکه، شرکت سیرجان ایرانیان، شرکت گل گوهر، شرکت فولاد کاوه جنوب، شرکت فولاد هرمزگان و بعضی دیگر از شرکت های فولادی اقدام به ارائه خدمات و رفع نیازمندی های کارفرمایان می نماییم.
وی اضافه نمود: برای تأمین قطعات خارجی با توجه به زمان ثبت سفارش، ساخت قطعه و بحث های انتقال ارز به حداقل 6 تا 8 ماه زمان نیاز است درصورتی که با توجه به پیش بینی های اجرا شده در این شرکت زمان تأمین بخش عمده قطعات سه هفته است. با توجه به تجارب پیشین در این واحدها بیشتر قطعات را تولید و انبارش کرده ایم و حتی بعضی از قطعات را طی 24 ساعت تحویل می دهیم و برای بعضی از قطعات نیز در بازه حدبیشتر 3 هفته ای کالا تحویل می شود.
نظری تأکید کرد: یکی از مهم ترین قطعات کمپرسور آب بند (Mechanical Seal) است که بر اساس تجارب سال ها بهره برداری و تعمیر این قطعه، تغییراتی را در آن ایجاد کرده ایم که باعث شده مکانیکال سیل ساخته شده از طریق این شرکت برای مدت چهار سال و بدون هیچ مسئله ای در سرویس قرارگیری، در سنوات گذشته کارهای زیادی اجرا شده که بار اصلی آن روی دوش آقای مهندس آستانه بوده و من افتخار دارم تا در این شرکت همکار ایشان باشم.
آموزش تعمیر و نگهداری کمپرسورهای گاز پروسس واحدهای احیاء
نظری تأکید کرد: با توجه به شرایط تحریم و عدم امکان آموزش نیروهای نوالورود به صنعت در خارج از کشور، یکی از ارزنده ترین خدمات شرکت پیشگامان صنعت آسیا تدوین دوره های آموزش تعمیر و نگهداری کمپرسورهای گاز پروسس واحدهای احیاء است که این دوره ها به شکل تئوری و عملی برگزار خواهد شد که هدف آن در کنار آموزش نیروهای شاغل در شرکت های فولادی کاهش زمان های توقف و افزایش راندمان شرکت ها از راه است.
وی در انتها اضافه نمود: این دوره ها در حال حاضر به شکل داخلی و در سال آینده برای کلیه شرکت های متقاضی قابل ارائه است.
منبع: خبرگزاری پانا